Princeton Researchers Develop A New Method For Building Soft Robots
Typically when we think of a robot, we think of a machine made from rigid plastics or metals such as the type typically used in a factory setting. While rigid robots do have their place, there are also situations where a soft robot is much more useful. Significant amounts of research are being put into creating soft robots today, and researchers from Princeton University have invented a new way to make soft robots called bubble casting.University researchers describe their method as utilizing "fancy balloons" that can change shape predictably when filled with air. Their new method injects bubbles into a liquid polymer causing the material to solidify and inflate, allowing it to bend and move. Utilizing the method, the researchers have created gripping hands, a flapping fishtail, and other devices. The goal is to utilize their new method to create new types of soft robots.
Soft robots are particularly useful in certain scenarios, such as picking orders and placing them in a box and other tasks. Soft robots are also seen as much better for situations where they will operate alongside humans. Rigid robots pose a significant risk of harm for humans that is eliminated by utilizing soft robots. Rigid robots are also typically unable to handle particularly fragile items such as fruits, vegetables, or eggs.
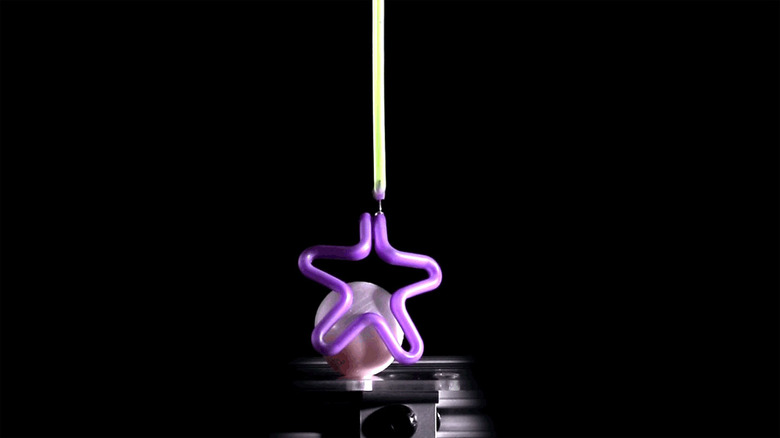
Soft robotics is also expected to have a place in healthcare in the future, with potential usage scenarios including wearable exosuits to help with rehabilitation, among others. One of the most difficult aspects of designing soft robots is how to control the way they stretch and deform. How soft robots stretch and deform controls how they move, and they hold the potential to move and expand in many ways.
The method created at Princeton relies on a liquid polymer called an elastomer. The elastomer cools into a rubbery and elastic material and is shaped by being injected into a mold. The mold can be in a myriad of shapes, including a simple drinking straw or complicated shapes like spirals and others. Next, the researchers inject air into the liquid elastomer creating a long bubble that expands the length of the mold.
Gravity causes the bubble to rise to the top, and the elastomer drains to the bottom of the mold, and once it hardens, it can be removed and inflated with air. When inflated with air, the side with the bubble stretches and curls into the thicker base. How the soft robot deforms is controlled by controlling how much time is allowed for draining during the curing process. Allowing the elastomer to cure more creates a thinner film at the top.
The thinner the film, the more stretching occurs as it's inflated, leading to more bending. Researchers can control various factors, including the thickness of the elastomer cooling in the mold, how quickly the elastomer settles to the bottom of the mold, and how long it's allowed to cure dictate how the elastomer moves once it's complete. Researchers say fluid mechanics is doing the work for them.
One of the more interesting designs is the star-shaped in the image above. When it's inflated, the arms of the star create an effective gripper able to grasp objects for lifting. The researchers also designed soft hands able to grip a blackberry, a coil that contracts like a muscle, and fingers able to curl individually as air is applied. Researchers point out they can predict how a shape will move using an equation they say can be used by anyone. It's also worth noting that their method does not require a 3D printer or other expensive tools.